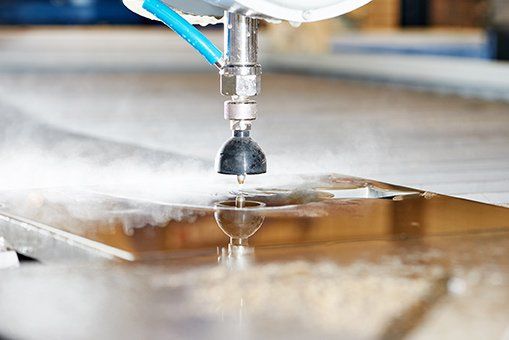
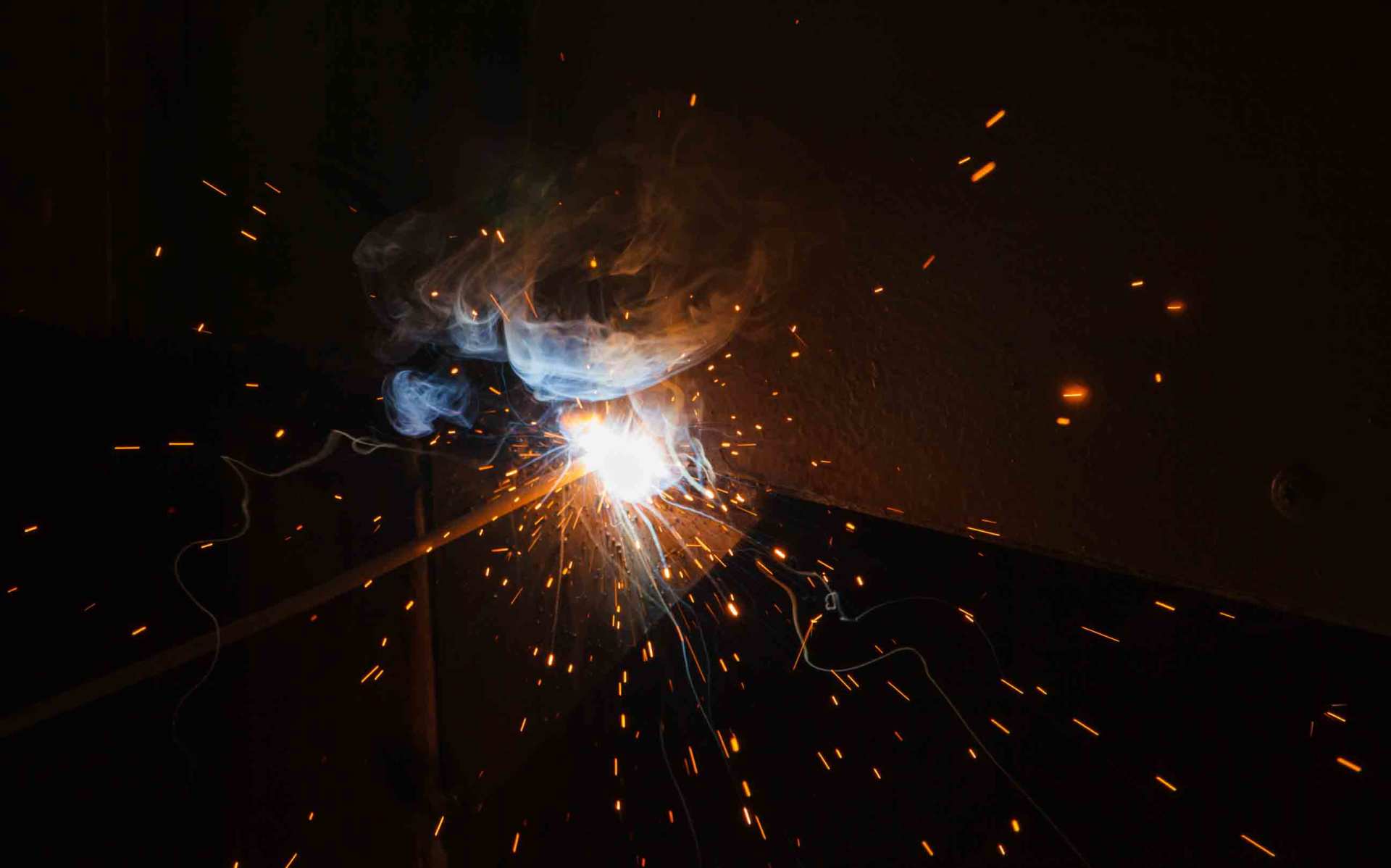
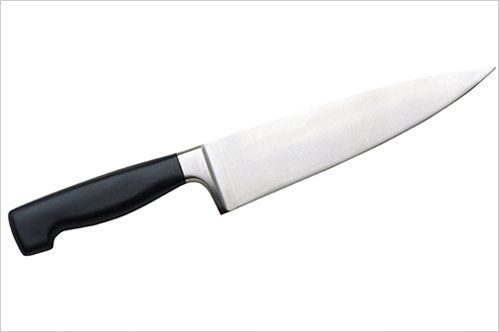
Steel holds an abundant place in the modern world. You can find steel anywhere from automobiles to high-rise buildings and industrial processing equipment. Many different types of steel exist, each of them being a slightly different alloy with iron as its base metal. Manufacturers then add other elements to boost the overall performance of the hardened steel.
Virtually all steel produced today contains the element known as manganese. Yet even within the metalworking world, many people fail to understand the role manganese plays in steel production. Discover three beneficial effects that manganese creates when you mix it with steel.
Manganese is a naturally occurring metal that people first discovered in 1774. On a chemical and physical level, manganese bears a close resemblance to iron, with manganese being harder yet also more brittle than iron. Manufacturers incorporate different amounts of manganese into the steel, depending on the particular type.
Certain varieties of stainless steel may have a manganese content of as high as 19 percent. In all cases, manganese greatly improves the hardness of steel, although not to the same extent as elemental carbon. In fact, manganese and carbon work hand in hand to improve the properties of steel.
Specifically, manganese improves what metalworkers refer to as hardenability, which governs how deeply the hardening effect penetrates. Manganese improves hardenability by lowering the critical cooling rate.
Lower critical cooling rates help avoid unwanted substances like ferrite and cementite, ensuring a more optimal chemical structure. In this regard, manganese improves the strength of steel.
Manganese also improves steel in terms of its hot workability. This phrase refers to the ease with which a metal bends under high-temperature conditions. Without manganese, steel often falls prey to hot shortness, which makes steel brittle at high temperatures.
Manganese reduces hot shortness and improves workability by preventing chemical compounds known as iron sulfides forming. When the steel alloy contains sufficient amounts of manganese, sulfur atoms do not bind with iron. Instead, sulfur reacts with the manganese to form much less detrimental molecules of manganese sulfide.
Manganese sulphide remains solid even at the extreme temperatures required for hot working. As a result, workers can more easily shape the steel. Without manganese, manufacturers could not machine steel whatsoever, as it would excessively liquefy. By sequestering the sulfur, manganese also prevents cracking or tearing during high-temperature steel development.
Oxygen poses a serious risk for iron-containing metals. Oxygen reacts with steel to form iron oxide — more commonly known as rust. This corrosion weakens the strength of the metal. Oxidation proceeds at a much more rapid pace when steel exists in its molten state. Manganese provides essential protection through deoxidation.
Manganese readily reacts with any dissolved oxygen in the molten metal, resulting in relatively harmless oxides forming. These oxides float up to the surface of the molten steel, where workers can easily remove them. While manganese deoxidizes steel quite readily on its own, manufacturers can achieve even more thorough results by adding silicon or aluminum as well.
Manganese has a vital role in the world of steel manufacturing, being the second most common alloying agent after elemental carbon. Up to 90 percent of all the manganese consumption today stems from iron and steel making.
For more information about how manganese helps metalworkers achieve strong and lasting results, please contact the steel fabrication experts at Knowlton Industrial Steel Supply. We are happy to answer your questions about any steel process or service. We also can do custom projects and provide same-day service. You can rely on our more than 30 years of experience.