Ways to Mitigate Metal Corrosion in Your Industrial Plant
- By Admin
- •
- 25 Jun, 2018
- •
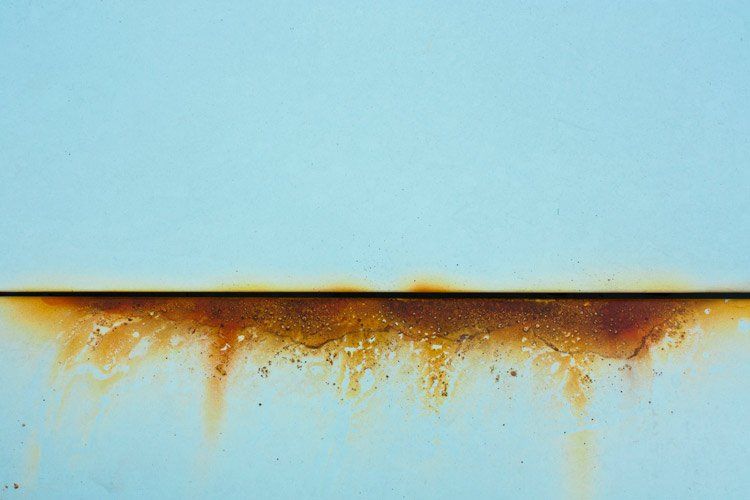
Corrosion is a significant concern in industrial applications where metal is the primary material in use. Widespread corrosion can increase maintenance and operational costs and prolong downtimes due to faulty equipment. The good news is that even though most metals are prone to corrosion, prevention is entirely possible.
Read on to learn about metal corrosion and ways to prevent rust in your plant.
Metal Corrosion Basics
Metal corrosion is an electrochemical process. Each metal structure has an anodic end and a cathodic end. Corrosion begins at the anodic end with the oxidation of ferrous ions. The anode end releases electrodes that travel through the metal to the cathodic end of the metal structure.
At the cathodic end, the electrons combine with water and oxygen to produce hydroxyl ions. The hydroxyl ions interact with the ferrous ions from the anodic end to produce ferrous hydroxide. When ferrous hydroxide mixes with air, the result is red rust, also known as hydrated ferric oxide.
Metal Corrosion Causes
Corrosion requires oxygen, moisture, and the presence of two dissimilar metals.
Oxygen and Water
Oxygen facilitates the oxidation of ions while water acts as the electrolyte through which current from the anodic end travels to the cathodic end. Unsurprisingly, metal tends to rust much faster in wet or humid environments. Additionally, airborne pollutants such as chlorides and sulfates can increase the rate of metal corrosion.
Dissimilar Metals
When two dissimilar metals, such as zinc and steel, interact, one metal corrodes and protects the other one from corrosion. In this case, zinc would corrode and therefore protect the steel.
The way each metal behaves depends on the level of the metal's reactivity in the presence of an electrolyte such as water.
Bear in mind that rust can form on a metal even if the metal is not in contact with another metal. This process is known as localized corrosion.
Metal Corrosion Prevention
Plant managers can implement several techniques to prevent corrosion. The most common methods include coating, impressed current method, sacrificial anode method, and use of chemical inhibitors.
Coating
Coating can be an effective method of mitigating metal corrosion. Coating techniques include electroplating, painting, application of welded overlays, among other methods.
Coating works to protect the metal structure from a corrosive environment or substance. Metal coating is a precise engineering process — be sure to find an experienced metal coating professional to get the job done professionally.
Impressed Current Method
In the impressed current method, metal experts use an electric power-rectifying device to generate an equal but opposing current against the corroding current from the anodic end. This lowers the voltage of the alternating current passing through the metal structure, thereby preventing the formation of rust.
Sacrificial Anode Method
In this method, a metal that is prone to corrosion is electrically bonded to another that is less prone, for protection. Galvanized steel is an example of the sacrificial anode method at play. Zinc, which galvanizes steel, is the sacrificial anode while the underlying steel is the protected cathode.
Chemical Inhibitors
Adding chemical inhibitors to a corrosive environment can slow down the oxidation and reduction process that constitutes corrosion. Chemical inhibitors can be in the form of gas, liquid, or solid compounds. Examples include tungstate, cathodic poison, and hydrazine among others.
Perhaps the most effective way to minimize the occurrence of corrosion in the first place is to assess your plant's environment to determine the metallic materials that are most compatible with the current environment. Understanding your environment can help to identify potential corrosives and find suitable ways to modify the prevailing conditions to mitigate rust.
At Knowlton Industrial Steel Supply, we supply a wide array of top quality metal products to suit the unique conditions in your plant. Get in touch with us today to find out how you can use our metal products to improve your operations.
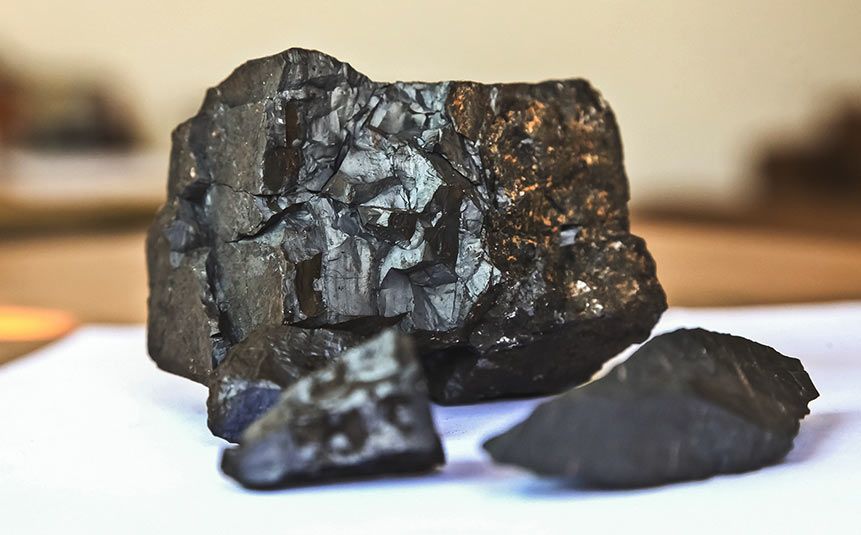
Steel holds an abundant place in the modern world. You can find steel anywhere from automobiles to high-rise buildings and industrial processing equipment. Many different types of steel exist, each of them being a slightly different alloy with iron as its base metal. Manufacturers then add other elements to boost the overall performance of the hardened steel.
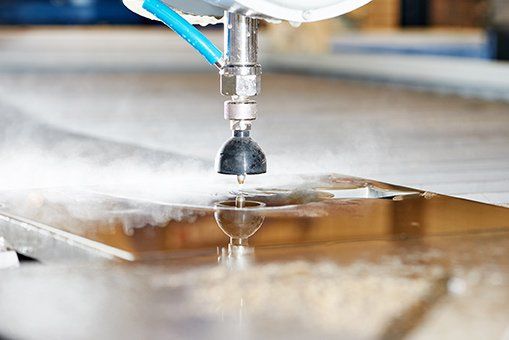
When you need to manufacture small or otherwise precise parts and tools, you face a wealth of options. Water jetting is a relatively new but increasingly popular choice among businesses, particularly if you work with dense or heat sensitive materials. Consider the following information about water jetting as you plan and design your components and the tools needed to work with them.
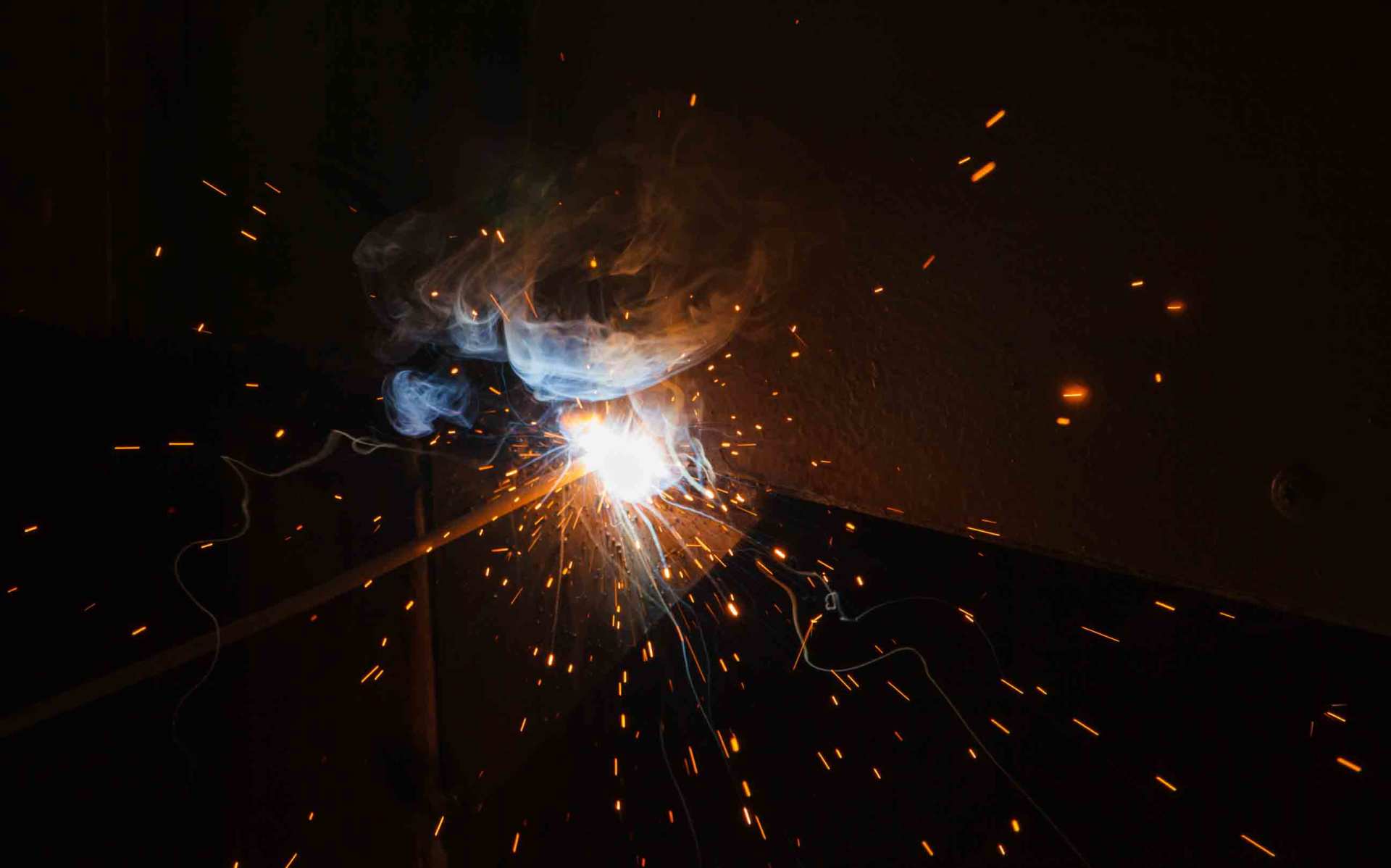
On the surface, the fundamental principle of welding is deceptively simple: high temperatures fuse together two or more pieces of metal. While this may be accurate in the most basic of terms, the actual art of welding remains much more complex. To get the strongest possible results, a welder must utilize the most appropriate welding method.
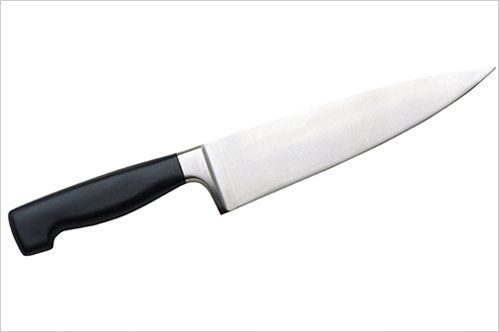
While knife and blade making is a skill many might associate with an era long gone by, it's one of the hottest growing DIY trends. Whether you want to simply use grinding tools to cut and polish a knife or feel ready to go all out with a forge and an anvil, you need the right kind of steel to get good results.