Post TitleThe 3 Types Of Steel Used For Knife And Blade Making
- By Admin
- •
- 28 Dec, 2017
- •
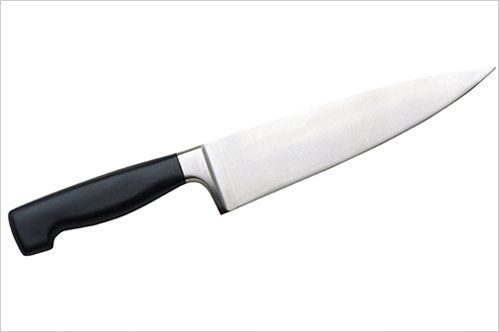
While knife and blade making is a skill many might associate with an era long gone by, it's one of the hottest growing DIY trends. Whether you want to simply use grinding tools to cut and polish a knife or feel ready to go all out with a forge and an anvil, you need the right kind of steel to get good results.
Yet there are thousands of different formulations and grades of steel to choose from. Before you pick an exact formulation, you need to understand the general types of steel that can be used to make durable and functional knives. Once you at least have a type narrowed down, you know where to start in picking a specific formula.
Tool Steels
The same grades and formulas of steel used to craft worthwhile tools like wrenches, drivers, and crowbars can be used to make high-quality knives. This is why it's such a popular project to use salvaged materials made from tool steel to forge knives and other blades without having to spend money on new stock. Of course, using new tool steel stock will be more reliable than reusing old materials because you know exactly what you're getting.
Most steel grades and formulas used for tool making are alloys that combine a small amount of carbon into the metal. Aside from carbon, tool steels often feature at least some chromium to give them a degree of corrosion resistance. However, they're still more likely to rust or corrode than stainless steel.
This is balanced out by increased hardness, better ability to hold an edge, and reduced chance to fracture during quenching or tempering. Some tool steels also include molybdenum and other additives to help the steel handle the stresses of extreme heating and cooling during forging or grinding.
Carbon Steels
While tool steel formulas contain some amount of carbon, they're not considered a high carbon steel. Grades like 1095 contain nearly 1% carbon in total, which gives the metal the highest amount of durability and strength without making it brittle or difficult to work. It takes an edge easily and stays sharp during heavy use, making it the best type of steel for survival knives, machetes, and other outdoor tools.
Since carbon steels don't usually contain many other alloy ingredients, they generally have the lowest resistance to corrosion. This is usually acceptable for heavy duty knives but will not work for cutlery or fine knives meant for display rather than regular use. Save the carbon steel for your survival projects and pay a little extra for an alloy with a good chromium content for those special designs you want to last.
Stainless Steels
Finally, stainless steel is not entirely corrosion proof, but it does resist the rusting and corroding effects that can weaken and discolor blades made from other grades of steel. However, it is also the most difficult to work, especially when it comes to heat treating and quenching the blade. In exchange for greater corrosion resistance, you also lose general hardness and may find that the blades lose sharpness faster.
For display knives, corrosion resistance wins out over the need for the knife to hold an edge during regular use. But for a survival knife, you'll need a high carbon content to maintain a good edge and hard spine while still using a stainless steel formula. Many knife makers investigate alternative ways to prevent corrosion, such as oiling the blade, rather than trying to find a stainless grade that fits their needs.
Regardless of which type of steel you need, we have it all in various bar stock sizes ready to work here at Knowlton Industrial Steel Supply.
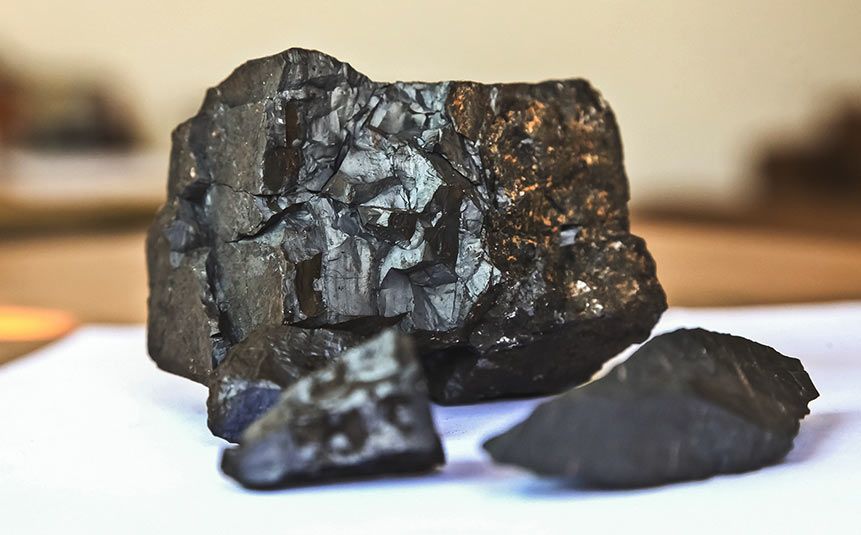
Steel holds an abundant place in the modern world. You can find steel anywhere from automobiles to high-rise buildings and industrial processing equipment. Many different types of steel exist, each of them being a slightly different alloy with iron as its base metal. Manufacturers then add other elements to boost the overall performance of the hardened steel.
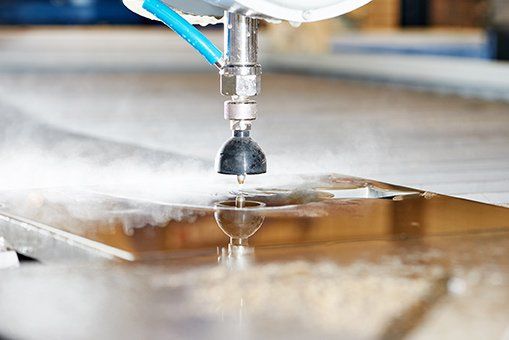
When you need to manufacture small or otherwise precise parts and tools, you face a wealth of options. Water jetting is a relatively new but increasingly popular choice among businesses, particularly if you work with dense or heat sensitive materials. Consider the following information about water jetting as you plan and design your components and the tools needed to work with them.
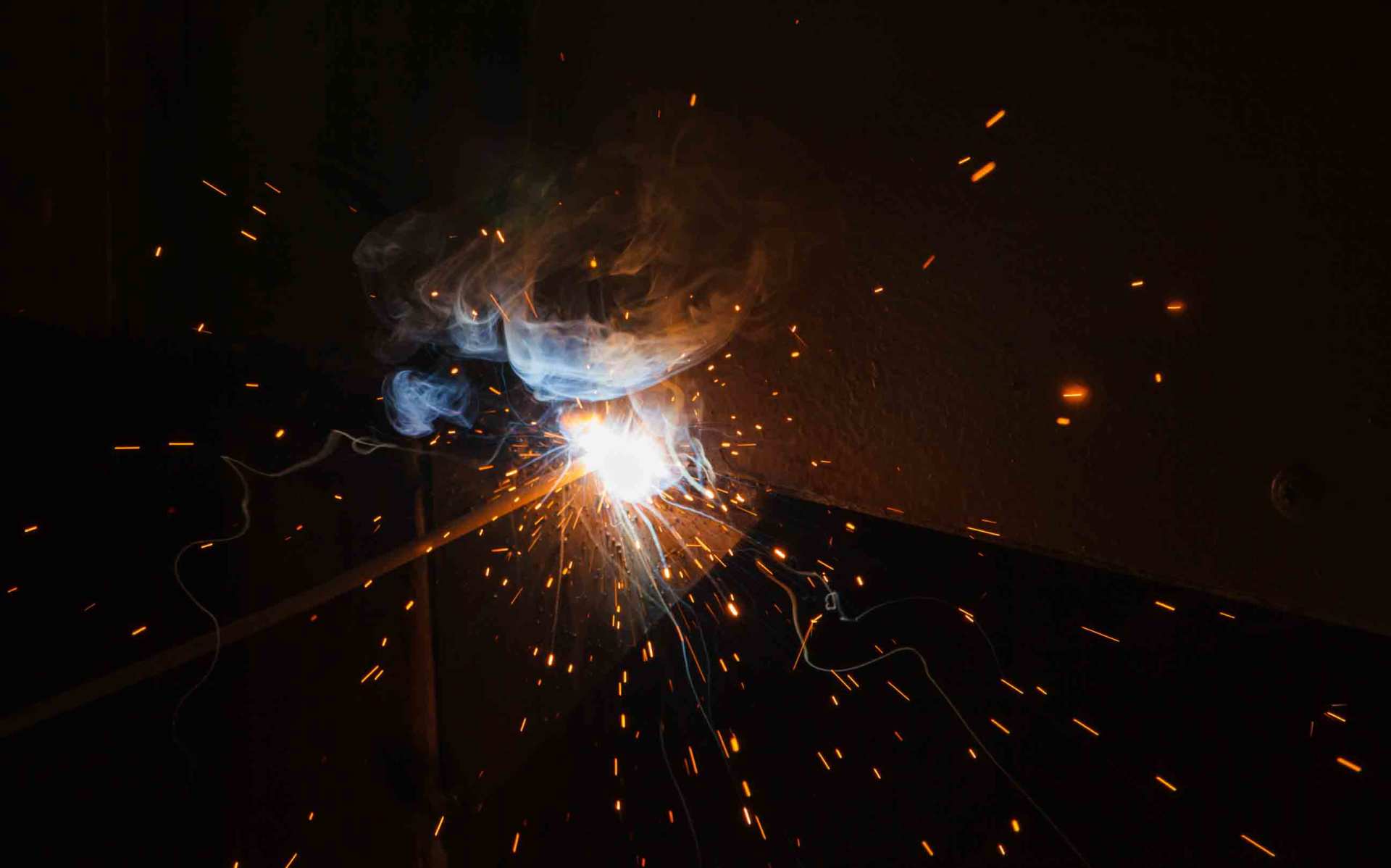
On the surface, the fundamental principle of welding is deceptively simple: high temperatures fuse together two or more pieces of metal. While this may be accurate in the most basic of terms, the actual art of welding remains much more complex. To get the strongest possible results, a welder must utilize the most appropriate welding method.